Unique curved staircase for luxury optician shop and eyecare centre
If you want to impress your clients with an astonishing interior design of your shop or restaurant, here is our proposal: an impressive modern curved steel staircase for luxury shops, able to make the most of the available shop surface.
Our oak and steel staircase with twisted architectural design is perfect to achieve an imposing elegant design.
London Stairs – Islington
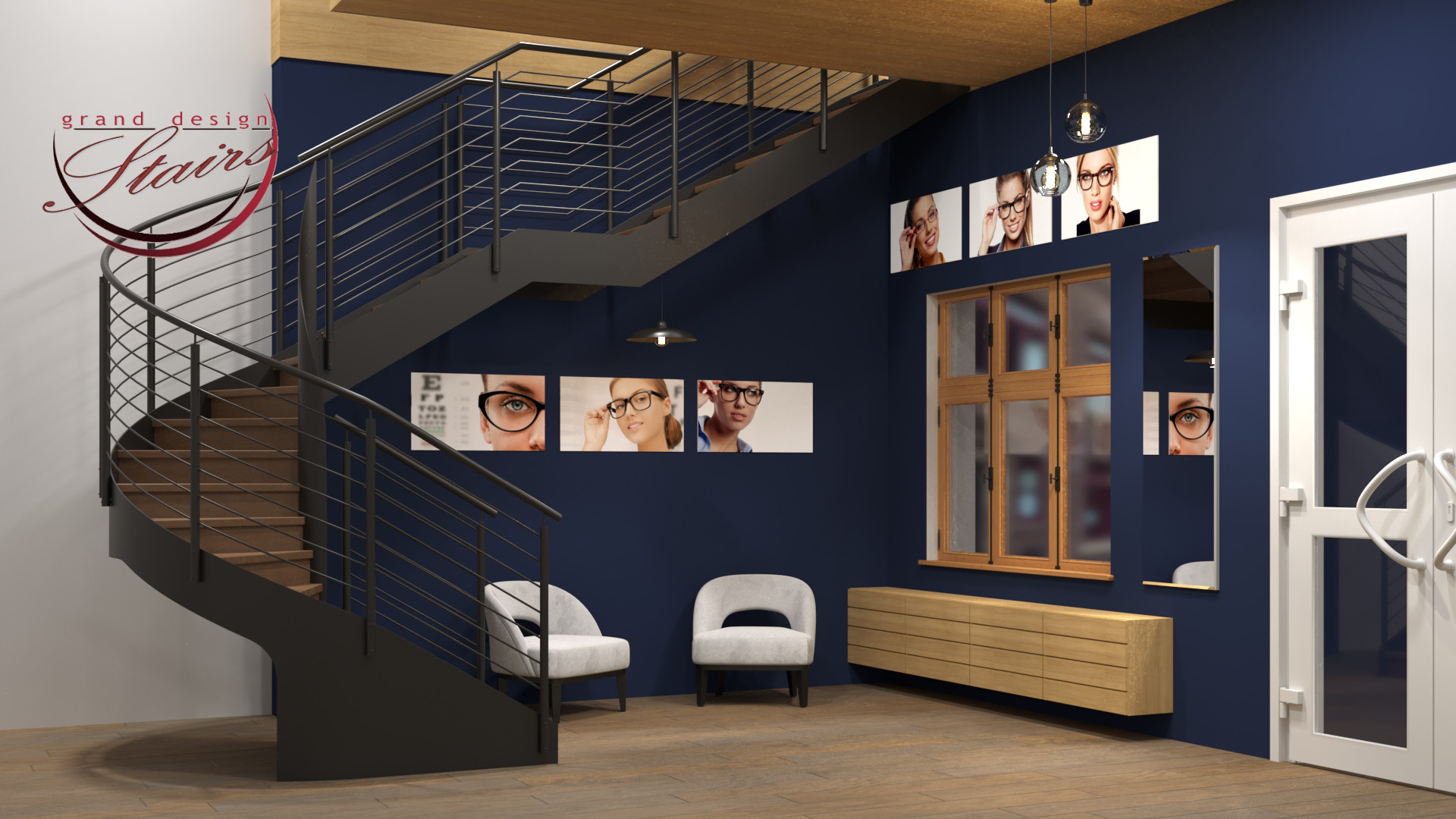
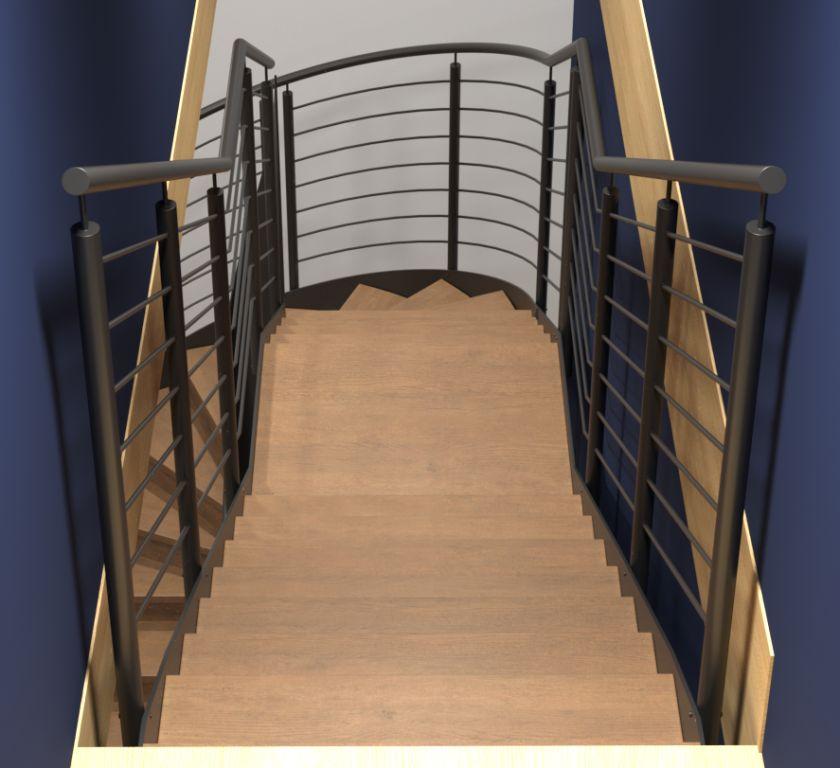
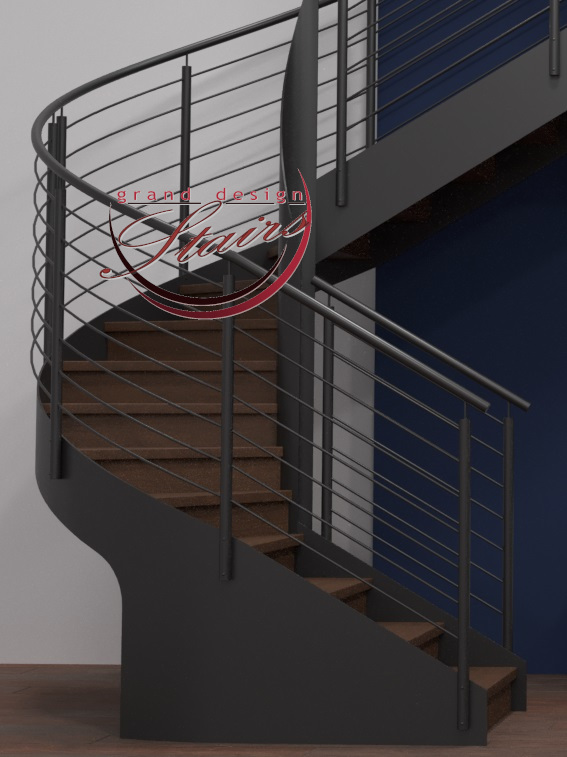
Staircase project ref. GDS Stairs – London – Upper Street, Islington – Unique curved staircase.
Our oak and steel staircase with twisted architectural design is perfect for tiny but unique homes. Here below you find more details on this project.
Staircase project details
Type of building: luxury Optician Shop and eye care centre
Staircase Architectural style: modern staircase
Location: Central London Islington – United Kingdom

Our clients say…
“In this project we worked with the Interior Designers to create a modern and functional space for our customer, an highly appraised Optician and Eyecare Specialist based in Islington – Central London. Grand Design Stairs team was instrumental to create a spectacular staircase in the limited space we had. We really feel we have reached the best quality at the best price. The expertise of Grand Design Stairs engineers and designers was a key factor to achieve the stunning result we wanted, an impressive and functional unique place.”
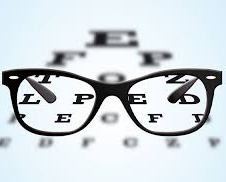
Adrian D.
Managing Director
Staircase Project Development – London Stairs – Islington
The contractor, a premium Interior Designer Group specialized in refurbishments in the fit-out sector, contacted Grand Design Stairs looking for a reliable partner to work side by side in the design and concept of a unique curved staircase to connect the ground floor reception and waiting rooms to the first floor eye care centre.
As often happens with Central London shops, the space available for the staircase was limited, but in spite of that the final staircase design had to be absolutely astonishing. In this case, we couldn’t impress the client with an helical staircase, but we had to conceive something different and unique.
Commercial Staircase Design
Being a commercial staircase used by a number of people, we also had to pay attention not only to the easiness of use, but also to the soundness and rigidity of the staircase and to the building regulations.
A traditional open staircase design or a helical or spiral staircase were not possible, due to the limited width we had. For those reasons we came out with a special design made by the bottom part to be a sort of spiral staircase with twisted centre pole and middle and top part designed as a straight flight with a middle square landing, which is a must on commercial staircases.
Choosing materials, colours and finishes
As for the colours and finishes, the client wanted to match some of the shop furniture elements and decided to have the steel staircase parts powder coated in satin black and the wooden treads and risers in oak.
The oak treads and closed risers had to match the oak floor. The customer delivered us a sample of the oak floor so that we could match the exact stain. We usually do some preliminary tests and show the samples to the clients for their approval before deciding the final stain and finish.
When the site was ready, with the concrete ground floor finished, the walls plastered and the top slab completed we were able to go back to site to check final measurements and agree final details to prepare the site with the site manager.
Once the final design and shop drawings were approved by the client, we could start production.
The staircase manufacturing took six weeks. All the staircase components were cut, crafted and pre-finished ready for fitting in the factory.
We always pre-fit our staircase in the factory to be sure that all components perfectly fit, so that the installation can be easy and straight forward. The fitted staircase looked monumental and impressive.
After last retouches, the staircase was disassembled and sent to the painting and staining departments.
Once painted, all stairs components were doubled checked before packing and preparing them for shipping.
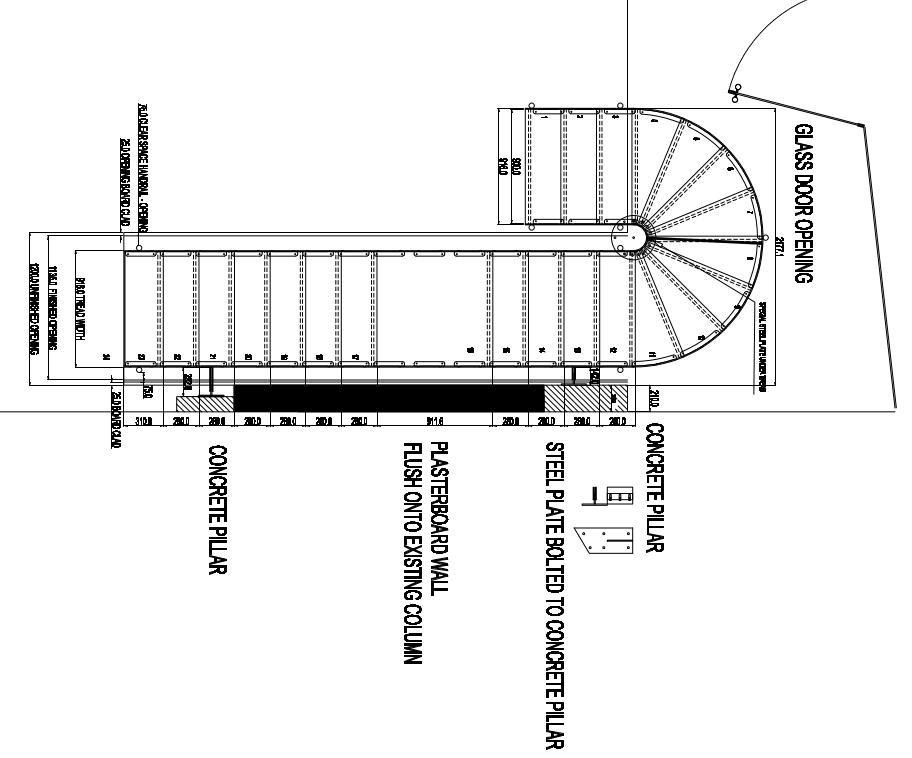
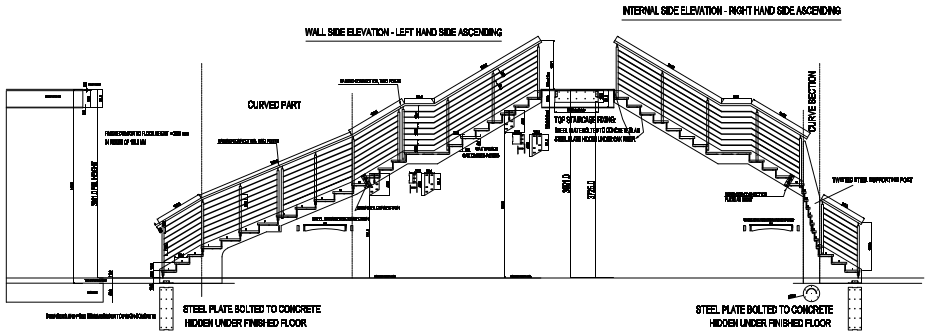
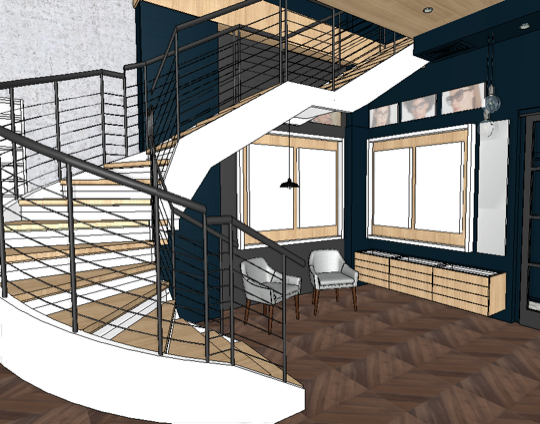
Staircase Design Features
The design was quite a complex one, as we needed to incorporate many risers to reach a height of 3990 mm, taking into account that the staircase opening was restricted to 1100 mm.
The architect proposed an initial possible design, which was approved by our engineers.
We introduced to the customers many options available in terms of materials, colours and finishes.
Instead of a soffit staircase, as originally planned, the customer follows our advice to incorporate the underside of the staircase in the whole interior design and have visible oak treads and risers.
Oak and black steel was decided for the furniture, therefore we suggested a powder coated steel balustrade to go all around the staircase.
We produced a 3D visual for the entire staircase design and sent some samples to the customer both for the oak treads, which had to match the oak flooring and the black powder coating. Once the customer was happy with our staircase concept and materials and gave his approval, we were ready to start production.
Staircase technical data sheet – London Stairs – Islington
Staircase Details | Clients preferred options | Other options & up-grades |
---|---|---|
Floor to floor height | 3991 mm | any measure available |
Ceiling opening | 1135 x 1200 mm | any measure available |
Risers | 24 @ 166 mm | 150 – 200 mm |
Staircase width | 916 mm | 900 – 1400 mm |
Staircase stringers | powder coated steel | stainless steel |
Staircase Treads & closed risers | oak | beech, iroko, walnut |
Railing model | powder coated steel handrail, posts & horizontal rods | curved glass railing |
Top Floor landing balustrade | walls all around the opening | Matching staircase railing or top mounted glass balustrade |
Steel staircase parts finishes | powder coated matt black | White, light grey, dark grey, rust effect or stainless steel railing |
Wooden staircase elements | brushed oak stained to client’s sample floor | beech, iroko, walnut smooth or brushed in different wood stains |
Additional items | LED lights on treads |
Order Process – How it worked – London Stairs – Islington
Step 1– staircase details
The interior designer called us and ask our help while working on a project in Islington – Central London, where her company was in charge of renovating an existing shoe store and converting it into a luxury optician shop. The project was at the very initial stage, so we could evaluate different possible staircase designs. The position of the staircase was however limited by the entrance door and the upper mezzanine. Previously we worked on an initial survey on site to have the basic measurements we needed to be able to start working on the basic plan staircase drawings. Afterwards we evaluated any works that had to be carried out on site in order to accommodate the staircase. After viewing the basic plans, the customer was able to decide the final layout and gave us information on materials and finished he wanted to use in the staircase.
Step 2- staircase quote
We sent our initial quote to the customer and he came back asking for some revisions. The budget he had available for the staircase was unfortunately a bit lower than the price on our staircase quote. At the same time, the interior designer informed us that he wanted to change the initial design, which has steel treads and closed risers structures with oak clad on top, to a simpler design with only oak treads and risers. We updated our quote accordingly and the customer was happy with it.
Step 3 – Staircase Concept Design
Straightaway we were then able to complete our initial stairs drawings and elevations and issue a 3D staircase visualization, so the customer and the interior designer could have a clear idea of how the staircase will be and how it will look in the shop. The customer was happy with it, and confirmed that the steel colour had to be matt black, while the oak stained to match the floors.
When the site was ready, with plastered walls and screed floors, we went back to site for a survey and double-checked the measures of our drawings. This second meeting on site was especially important has we could give information to the builders on how to prepare the site to receive the staircase. We asked to the builders on site to move some cables and pipes, since they were in the way and to reinforce the ceiling slab.
Step 4 – Staircase Production drawings
Our technicians and engineers reviewed the initial drawings and issued the shop drawings in an AutoCAD file accordingly, ready to be submitted to the customer, architects and building regulations inspectors for their final approval. Once approved, we started manufacturing.
Step 5 – Staircase Construction – London Stairs – Islington
We started the staircase construction working with the steel stringers on the laser-cut machine while our carpentry division was creating the wooden treads and risers stairs parts. We created the steel railing according to drawings, we weld and satin-finish it.
The entire staircase was then pre-fitted in the factory and prepared for painting and finishing. All components are carefully checked and prepared for an easy and straightforward site installation.
Step 6 – Staircase shipment
Due to the length of the stringers (two of them being 5 m long), volume and weight we had to book a dedicated truck to collect the package from the factory and go directly to the site in Islington – Central London.
We provided a detailed packing list, so that upon staircase delivery, the customer could check that all stair parts were delivered and all was ok.
Step 7 – Staircase Installation – London Stairs – Islington
We had a team of three people on site working on the installation for three days. Since the fitting team had previously perfectly organized on site, with lifting equipment available for the installers to lift the heavy stringers, installation was quick and straightforward.
Initially the installers began fitting the steel stringers and the twisted centre pole and fixing them to the floor, to the existing concrete pillars and to the top slab. Then it was time for the oak treads and risers. The steel railing was the last. Since all components were pre-fitted in the factory, they could have been easily installed. Last thing to do was cleaning the site and that’s it! The magnificent staircase finally on its place, ready to receive appreciation comments by the customers visiting the luxury shop.
Get started with your staircase project …